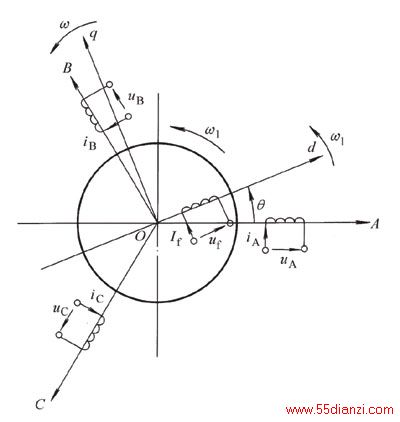
三相定子绕组静止电气方程:
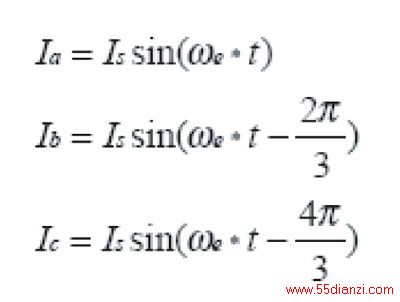
三相定子坐标系到两相静止坐标系的变换方程(Clarke变换)
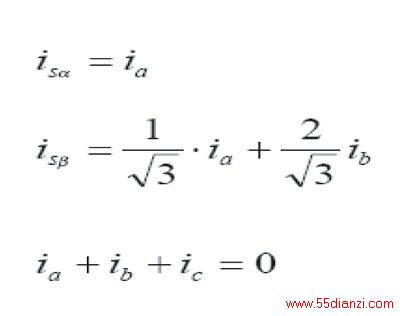
静止坐标系到转子同步旋转坐标系的变换方程(Park变换)
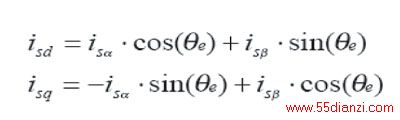
Park逆变换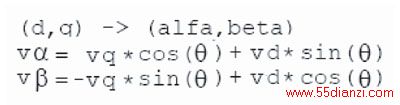
Clarke逆变换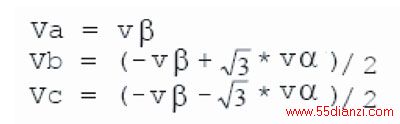
α和
β两相静止坐标系变换成同步旋转磁场定向坐标系d、q如图4
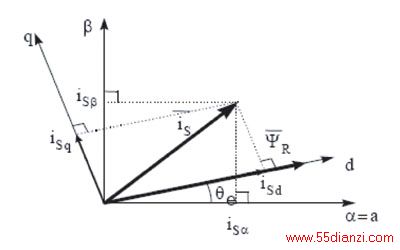
同步电机采用改进的空间矢量磁场定向控制策略,控制系统采用速度环和电流环双闭环结构,电流环采用PI调节器,实现简单,并能获得较好的电流跟踪性能。速度环采用PI调节器,能有效地限制动态响应的超调量,加快响应速度。系统采用转速、电流双闭环调速系统;系统全数字式的关键是电流环数字化,就是把数模混合式变频系统中的模拟电流环,采用数字方式加以实现,其核心提高电流环的处理速度,达到或接近模拟电流环的响应速度。根据目前的微处理器DSP、A/D器件的水平,可以满足硬件的需要;另一方面在于控制策略及控制软件的优化。良好的系统硬件和软件设计是使研制的系统达到实用化的保证,在满足性能要求的基础上,必须充分利用硬件资源,提高集成度降低硬件成本,达到产品化的目标。 矢量控制系统的解耦, 速度给定ω与速度反馈相减得出速度误差,速度误差经PI调节后输出转矩电流给定iq,id励磁电流给定是根据系统的动态需要进行调整其值根据不同的电机和负载得出的经验值,电机三相电流反馈ia、ic、ib经传感器采样,然后再根据转子位置电气角度θ进行Clarke变换,变换后输出ialpha、ibeta, ialpha、ibeta经Park变换输出id、iq,id、iq值与给定值iqref、idref求误差,进行PI调节后输出Vq、Vd, 电压矢量和转子位置电气角度θ经过Park逆变换Clarke逆变换输出电机定子三相电压Va、Vb、Vc值,三相电压Va、Vb、Vc值作为PWM(脉宽调制)的比较值比较输出PWM波形到逆变器然后驱动电机旋转。 整个系统的控制原理框图如上图5所示。
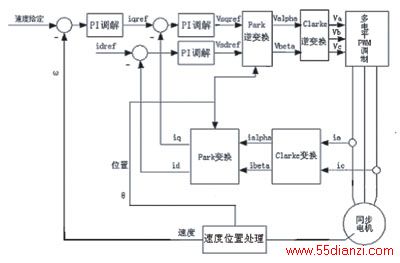
图5 矢量控制原理图 本方案的同步电机的励磁电流是If是按照固定励磁电流给定方式工作,对于同步电机的转子励磁电流If的给定,通过对同步电机的空载特性试验和短路同性实验,测出电机的各项参数并计算出所需运行的额定励磁电流,此时根据额定的励磁电流If调节定子侧的去磁电流Idref就可以调节系统的功率因数,功率因数角δ=arctan(iq)/(id),控制Idref就可以使得系统是运行在功率因数超前还是滞后。
1)硬件主控实现部分 系统的软硬件控制如图5,由DSP数字信号处理器作为主控CPU,可编程逻辑器件实现部分算法的计算和波形发生及各种信号的处理,AD采样处理电流电压反馈信号并传到DSP,单元与主控板CPU的通信采用光纤串行高速通信方式,单元的状态信息经可编程逻辑器件进行串行编码后通过光纤发送到主控制器的接收板,主控制器接收板进行串行到并行解码后传输到主控CPU;主控CPU根据单元状态信息,调整系统的控制状态;速度与位置传感器的信号经传感器板可编程逻辑器件进行串行编码后经高速串行传输到主控器板的可编程逻辑器件,可编程逻辑器件对传感器反馈的速度位置信号进行运算处理,测速方式采用变M/T测速,可以实现高精度的测速要求,可编程逻辑器件计算出速度和位置的有效值,并对传感器检测有无故障状态,上报主控CPU,同时主控CPU可以根据测速的要求动态调整测速方式和时间;本系统中的电流检测元件选择了根据磁场补偿原理制成的霍尔效应电流互感器,以满足实时监测电流的要求,电机的三相电流和电压信号经信号调理电路处理后,变成模拟电压信号输入到主控板的AD转换芯片,该AD芯片可以在瞬时情况下对三相的电压电流信号进行采样保持并转换,这样能保证真实的再现电机瞬态三相电压电流的波形,AD转换芯片采样完成后上传三相的数据;主控制CPU与上位系统采用的是RS232通讯模式,实时的接收上位机给定的各项参数设定值,并上报整个系统的运行状态和各项数据;系统的外部I/O输入输出经隔离传输到主控CPU的I/O口,主控CPU根据控制要求作出相应的执行控制;AT25128是串行EEPROM与主控CPU通信采用SPI方式,EEPROM主要起着保存上位系统各项设定参数值和存储系统的一些运行状态信息;主控CPU采用的是DSP 它是TI公司C2000系列的TMS320LF2407A,DSP是一种高速的微处理器,其最大特点是运算速度快,比目前16/32位微处理器和单片机的运算速度至少快一个数量级,DSP这种高运算处理能力能够满足电流环实时控制的高要求,可以同时对电机的转子位置和速度进行辨识以实现无速度传感器矢量控制要求,并且可以采用先进的现代控制策略,获得更高的控制性能,更完善的功能;整个硬件的原理框图如图6所示。
2)可编程逻辑器件的实现原理 单元模块与主控制器的通讯采用光纤串行高速通讯模式,其通讯速率为4MHz这样可以满足实时控制要求,每个模块与主控制板通讯采用双工模式,可编程逻辑器件发出的PWM波形信号经编码后并串转换,通过光纤驱动发送到单元模块,同时可编程逻辑器件接收单元的串行编码进行串并转换,把单元的状态信息和故障信号以中断方式上传给主控DSP,具体如图7。
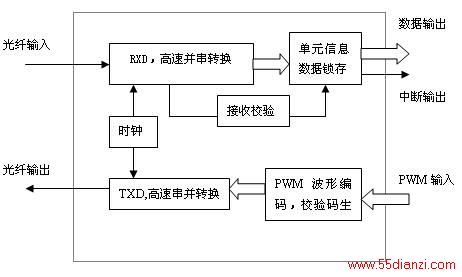
图7 单元通信处理模块 传感器信号的测速,对串行输入的编码进行解码输出电机转子的位置信号数据,根据传感器的转速脉冲信号进行测速,测速方式采用变M/T测速,根据测速的M值与T值进行数据运算得出转子的转速,由于采用了可编程逻辑器件硬件逻辑测速方式,使得测速范围很宽和精度很高,能够满足系统精度要求。 PWM信号生成,根据DSP运算输出的的数据可编程逻辑器件用高速时钟生成数据,并进行单元串联的PWM波形移相,输出到光纤发送模块。 由于系统采用全数字化控制方式,所有的控制策略全由软件编程来实现,因而,软件的设计决定着整个系统的性能。控制策略采用转速、电流双闭环系统,其中转速环采用PI调节、电流环采用PI调节,算法由DSP数字信号处理器软件编程实现。速度环的输入是速度反馈和速度给定的差值,输出作为电流环的给定。电流环的输出来控制PWM波形生成器,所生成的PWM波形控制逆变器中功率开关器件的通断,以实现对电机的调速。整个软件处理系统采用前后台处理模式,程序的中断服务采用嵌套处理的形式,以保证整个系统实时信号的处理,中断源有4种,包括系统保护中断,片内电流环定时处理中断,速度环定时处理中断,外部通讯中断; 软件系统上电进行初始化,关中断清各种标志位,配置DSP的各个外设模块和I/O口,读取EEPROM中的参数信息,计算电机的位置信号和电角度,延时检测高压上电否?进入系统主循环;系统保护中断,检测单元模块的故障状态和系统的保护中断,在出现过流、过压、PLC等故障时,系统关断IGBT的输出并停机上报系统的故障信息; 系统主流程,系统上电后,对系统的RAM空间和各项外设模块进行参数设定,对RAM清零,接着对外部I/O和PLC进行复位初始化,从EEPROM中读取初始电机的转子定位信息,检测高压是否就绪如就绪开放各种中断进入主循环,否则一直检测高压就绪状态信息直到高压就绪。主流程如图8。图8 主程序流程图
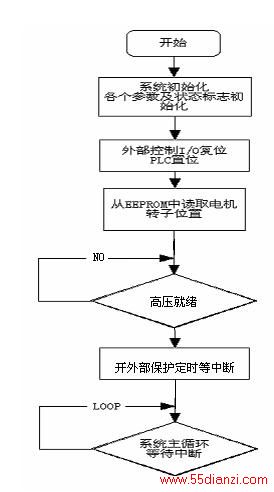
上一页 [1] [2] [3] 下一页
本文关键字:变频器 同步电机 产品选型,变频技术 - 产品选型